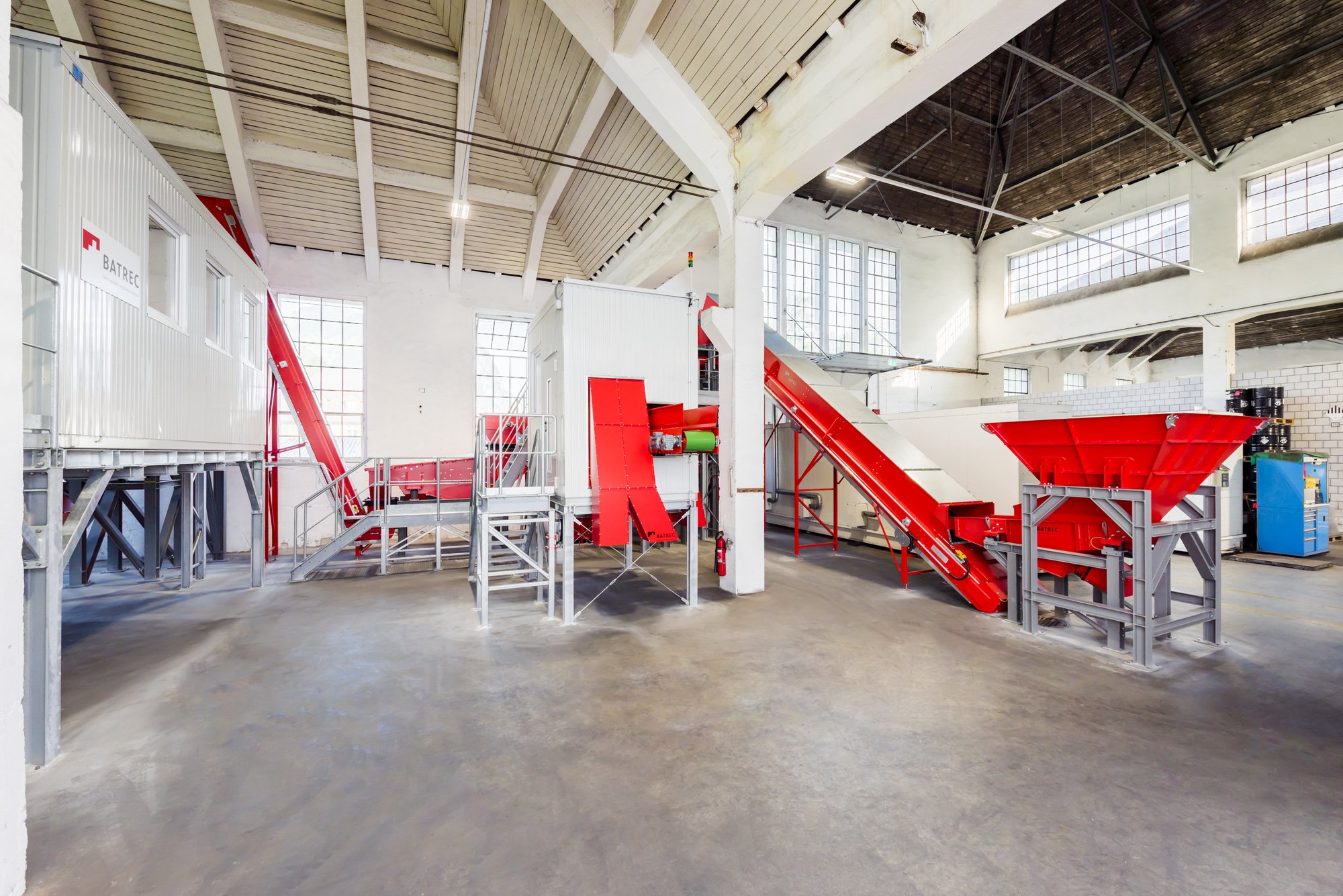
Recycling batteries
The recycling of all collected end-of-life batteries is mandatory according to the provisions of the battery directive 2006/66/EC.
Because there are various types of batteries, all having a different chemical composition, several specific recycling processes are used depending of the chemistries. For example, a recycling process for alkaline batteries is not suitable for recycling Li-ion batteries.
For portable batteries, the collection systems usually gather all types together without distinction. Therefore a sorting step is necessary before the recycling step itself.
Introduction
Portable batteries have different size, form, weight… They have different markings on their outer surface but not always allowing a perfect recognition of the type/chemistry.
The objective is to sort the portable batteries per chemistry as the recycling processes are usually devoted to a specific battery chemistry.
Fortunately, the internal design of a battery is usually specific to a chemistry. This property is used (in combination with other characteristics) for sorting batteries on an industrial scale;
Here is an overview of the main sorting methods used:
Sorting By hand: based on the size, dimension, labels…
Sorting by x-ray : an Z-ray scan of the batteries reveals their internal design and can be used as a sorting method.
Sorting by electromagnetic properties: here also the magnetic scan of a battery reveals its internal construction and can be used for sorting batteries per chemistries.
By a combination of the above: usually to achieve a very high level of quality / efficiency when sorting batteries, several parameters have to be combined (weigh, size, electromagnetic scan, etc.)
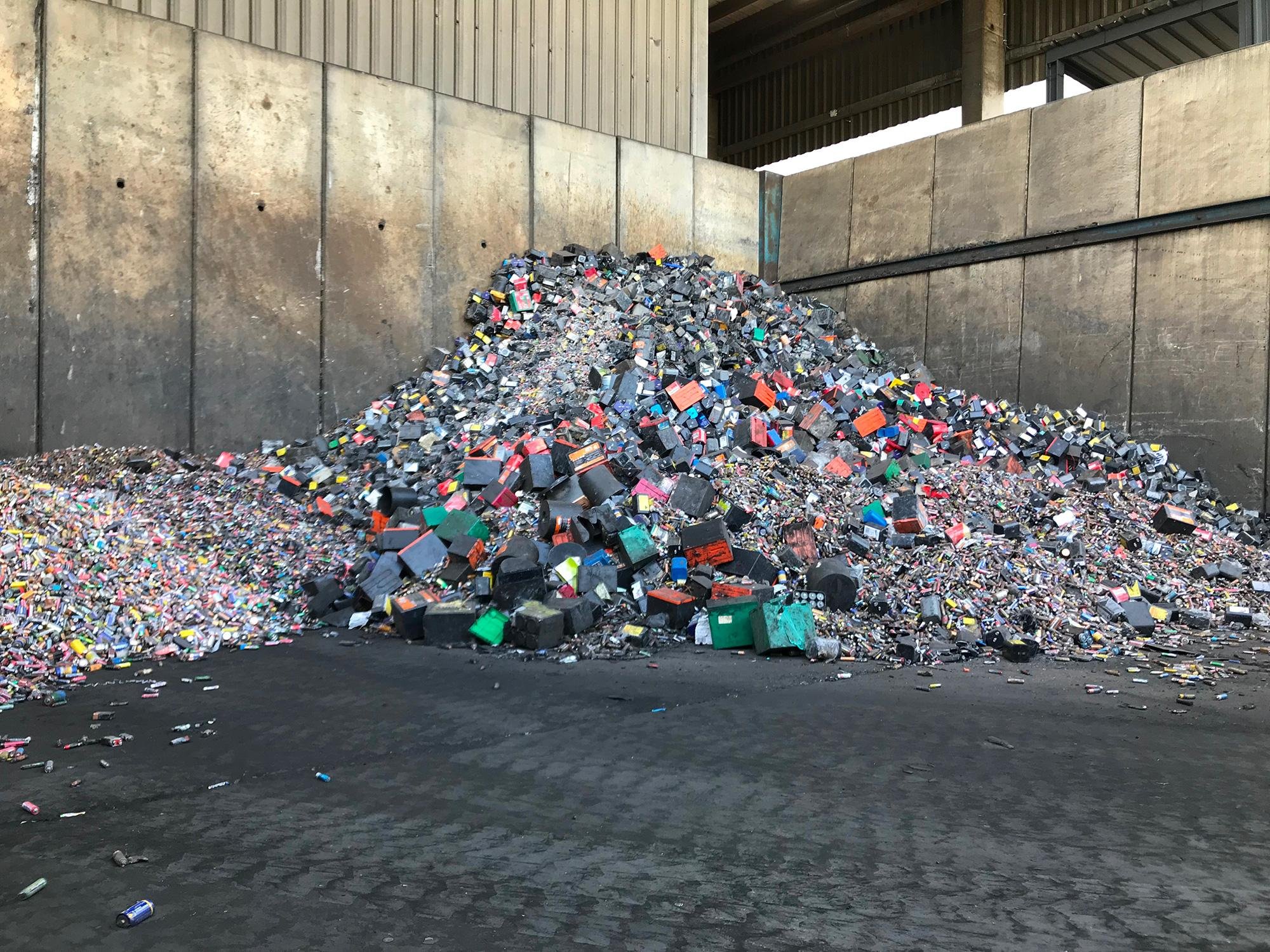
Recycling technologies for batteries
Each recycling process is unique. Even for the same type of batteries, several different processes may be used by recyclers. It is almost impossible to describe all the existing, industrialised processes in details. We can only described the main process families, knowing that an actual recycling process often combine several steps/technologies.
Here are the most important family of recycling processes:
Pyrometallurgical process
The batteries (or part of) are smelted in a furnace at high temperature to recover some metals (that can be re-used in the industry) and a slag.Hydrometallurgical process
The batteries (or part of) are dissolved in an acid or base solution, undergoing further chemical reactions till the production of high quality recycled materials that can be re-used.Mechanical process
The batteries are crushed or open in a way to recover some fractions directly (also called 'Direct recycling process').
An industrial recycling process is usually a combination of some of the above technologies. For example, after crushing the batteries, some fractions can undergo an hydrometallurgical process before being recovered to a level allowing their re-use in the economy.
Another example: a pyrometallurgical process can produced a combination of metals that will need further refining before meeting the quality requirements for re-used in the industry. The refining step can be hydrometallurgical for example.
Multi-step battery recycling technologies
Most recycling processes involves several steps, some of them not always taking place in the same location or performed by the initial recycler. We can speak of a battery recycling chain.
How far the recycling should go?
The battery directive 2006/66/EC stipulates the recycling rate to be achieved for batteries. For thjs purpose, the batteries are divided into 3 families, each having their own recycling targets.
Recycling targets
The calculation methodology, as well as the reporting system of the recycling rate achieved (called Recycling Efficiencies) is indicated in a separate European Regulation EU) No 493/2012 of 11 June 2012.
Note: the Battery Directive is currently undergoing a revision and the recycling targets may be updated in the future.